The backbone of any successful transport operation lies not in its vehicles, routes, or schedules – but in the people who bring it all together. Let’s explore how traditional transport teams create the foundation for logistics excellence, examining their operations and the challenges they face in the rapidly evolving digital ecosystem.
The Existing Team Structure
Traditional transport operations are typically organized around three core departments, each vital to the organization’s success. Let’s dive into the different department’s framework and their core functionality.
Fleet Management & Operations Team
Their main function is to oversee vehicle movements and ensure timely deliveries through manual processes and basic GPS tracking. It often involves extensive phone calls and paperwork to track fleet status, manage schedules, and handle unexpected delays. They are responsible for:
Maintenance Team
Their work to ensure the fleet’s roadworthiness and minimize downtime through routine inspections and reactive or manually handled proactive repairs. They rely on manual logs and physical records to track vehicle maintenance schedules and history, and also coordinate with drivers and suppliers for spare parts or servicing. Thus, they focus on:
Finance & Accounts Team
Their key responsibility is to manage budgets, track expenses, and ensure accurate billing in the logistics process. In a traditional setup, this involves manual bookkeeping, paper-based invoicing, and reconciling records with fleet operators and vendors. Their job responsibilities include:
Challenges they face in the evolving digital landscape
The traditional logistics industry struggles with compartmentalized operational structures, where different teams manage fleet management, maintenance, and financial data through separate systems. This fragmented approach creates significant operational challenges in today’s complex business environment. Critical information becomes isolated, leading to delayed decision-making and increased potential for inconsistencies through multiple data entry points.
Teams managing different operational aspects face considerable coordination challenges. Resource optimization becomes increasingly difficult as organizations struggle to balance maintenance schedules with operational demands. Traditional planning methods require extensive manual coordination, which significantly impacts the ability to allocate resources efficiently and maintain real-time visibility into operations.
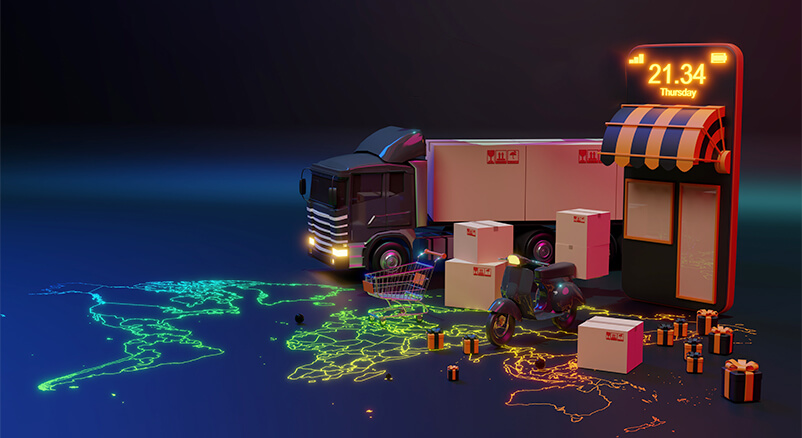
Reporting and analytics present additional hurdles in this fragmented environment. Consolidating data from various sources demands significant manual effort, making historical trend analysis time-consuming and complex. Performance metrics often require extensive reconciliation across different systems, potentially creating substantial gaps in organizational understanding and strategic decision-making.
Forward-thinking organizations are now embracing integrated digital solutions to transform their operational approach. These advanced technologies aim to streamline cross-departmental workflows, enhance real-time visibility, and support data-driven decision-making. By breaking down traditional operational silos, companies can create new opportunities for operational excellence in an increasingly dynamic logistics landscape.
In our next blog, we’ll explore how digital transformation is revolutionizing these traditional structures and creating new opportunities for operational excellence.